AC Servo Motor PCBA Solution for Industrial Automation
1. Background
With the rapid evolution of industrial automation, AC servo motors have become critical components in motion control systems requiring precise speed and position control. One of our European customers developing a new generation of AC servo motors faced several challenges: unstable control performance, high EMI risks, complex assembly, and unpredictable lead times. They sought a partner capable of delivering high-reliability PCBA manufacturing with rapid response and customization capabilities—that’s where KKPCB came in.
2. Application Scenarios
This PCBA solution is primarily applied in the control units of AC servo motors used in:
- Precision feeding systems on automated production lines
- High-speed position feedback systems in smart manufacturing equipment
- CNC machinery, packaging systems, and textile automation
- Industrial robots and collaborative robotic arms
- Elevators and building automation drive modules
3. Key Product Specifications
Category | Specification |
---|---|
Power Input | AC 220V / AC 380V (customizable per client system) |
Control Circuit | 32-bit ARM MCU + DSP co-processor |
Drive Output | 3-phase AC motor drive signal, max current 12A |
Communication | CANopen, RS485, Modbus RTU, EtherCAT (optional) |
PCB Size | 190mm × 130mm × 1.6mm |
PCB Material | FR4 TG170, high-temp reliability material |
Assembly Class | IPC-A-610 Class E, SMT + THT hybrid process |
Protection Features | Overvoltage, undervoltage, overcurrent, short-circuit, overheating |
EMC Compliance | Meets EN 61000 industrial-grade EMC standards |
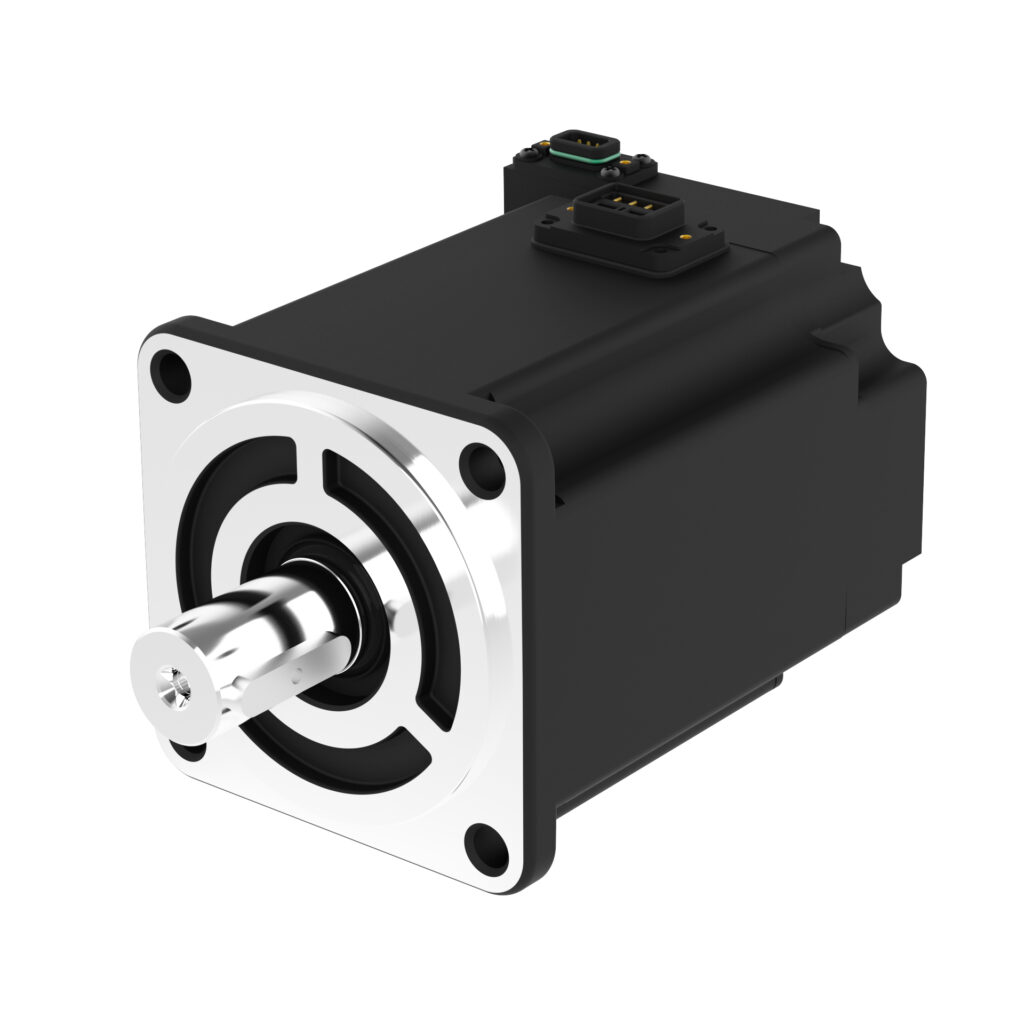
4. Results After Implementation
By working with KKPCB, the customer achieved substantial improvements in their servo motor control unit project:
- Quality improvement: Repair rate dropped from 2.5% to 0.6% with enhanced inspection (AOI + X-ray + functional testing).
- Cost reduction: BOM cost decreased by 11.8% through component optimization and local sourcing strategies.
- Performance upgrade: EMI issues were reduced by over 70% through optimized PCB layout and signal integrity controls.
- Lead time acceleration: Batch production lead time reduced from 8 weeks to 4.5 weeks, ensuring a faster time-to-market.
5. KKPCB’s Advantages in This Project
In this collaboration, KKPCB demonstrated its full-stack capabilities in PCBA manufacturing for industrial motion control systems:
- Over a decade of experience in industrial-grade PCBA for automation and servo applications
- End-to-end services: PCB manufacturing, component sourcing, SMT & DIP assembly, and functional testing
- Certified under ISO 9001, ISO 13485, and IATF 16949 for strict quality assurance
- Equipped with advanced testing gear like German Viscom AOI, X-ray, and FCT platforms
- Dedicated engineering support and logistics team for European customers
6. KKPCB’s Manufacturing-Focused Custom Solution
KKPCB provided a manufacturing-oriented, fully customized PCBA solution for the client’s AC servo motor application:
- PCB Design: Custom 6-layer structure with dedicated power and signal planes, enhanced heat dissipation for high-current loads
- Assembly Process: Double-sided SMT with heat sink soldering for IGBT and MOSFET areas
- Packaging Enhancement: Modular top-cover integration for better mechanical protection and EMI resistance
- Testing Support: FCT + high-voltage burn-in testing simulating end-use conditions for reliability assurance
- Sample Iterations: Three prototype rounds delivered within 7–10 days, helping client achieve EMC certification efficiently
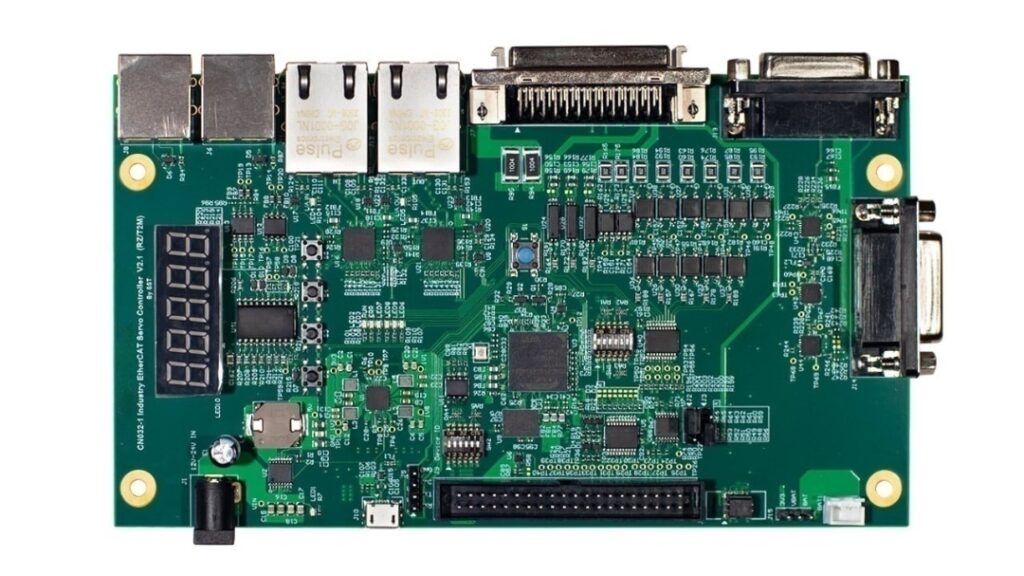
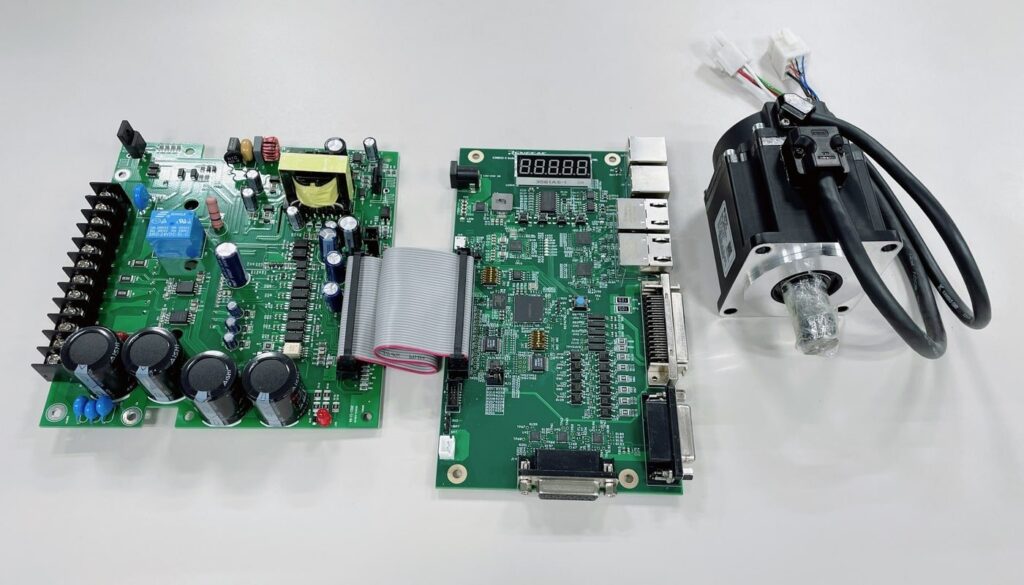
7. Actual Outcome of the Solution
- Delivery reliability: In three consecutive batches totaling 12,000+ units, defect rate was kept below 0.5%, outperforming industry norms.
- Functional consistency: 100% pass rate in system-level integration, with zero runtime errors during 1200+ hours of continuous testing
- Cost optimization: Through BOM savings and process improvements, total unit cost dropped by 9.3%
- Faster response: Parallel production management allowed first batch delivery within 15 working days, helping client launch 2 months ahead of schedule