Industrial Battery Charger PCBA Solution Case
— Customized Manufacturing Support by KKPCB for a European Client
1. Background Overview
In the field of industrial automation, battery-powered systems have become increasingly important, especially for uninterrupted power supply in mission-critical applications. A European client specializing in compact, high-performance battery chargers for automation systems was seeking a reliable PCBA manufacturing partner to enhance product quality, reduce costs, and improve delivery timelines.
During pilot production, the client faced several issues, including inconsistent soldering quality, thermal management challenges in power modules, high component costs, and layout inefficiencies. To overcome these challenges, they turned to KKPCB for a customized, industrial-grade manufacturing solution.
2. Application Scenarios
- Backup power supply in industrial automation systems
- Auxiliary power for PLCs
- Emergency/standby systems in building automation
- Power supply for actuators, relays, and edge devices
3. Product Parameters
Parameter | Specification |
---|---|
Rated Output Voltage | 13.8V DC |
Max Output Current | 11.0A |
Output Power | Up to approx. 152W |
Voltage Accuracy | Within ±1% |
Operating Temp. | -10°C to +50°C |
Efficiency | ≥88% |
Protection Features | Short-circuit, Overload, Over-temp |
Control Interfaces | Remote ON/OFF, Status Monitoring |
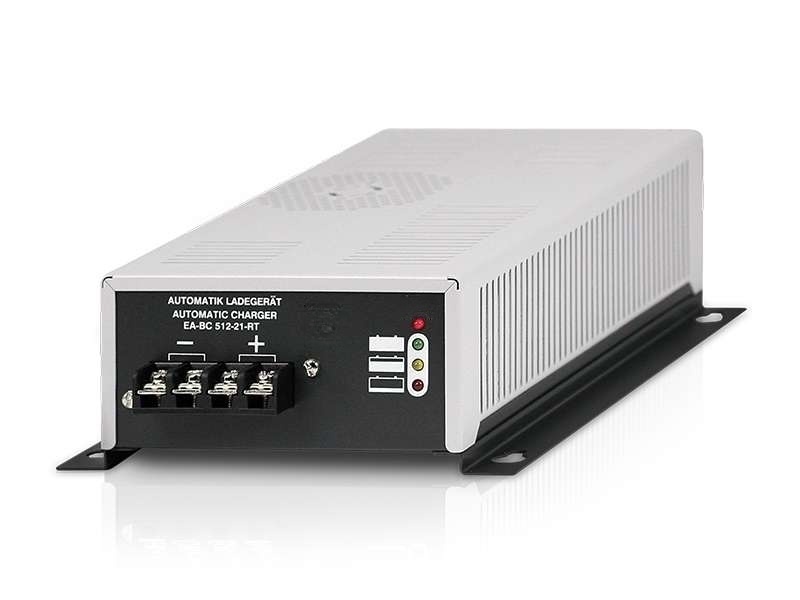
4. Implementation Outcome
After switching to KKPCB’s optimized manufacturing solution, the client achieved:
- Product yield rate increased from 94.2% to 99.3%
- PCBA production cost reduced by approximately 12%
- Average thermal output decreased by 17%
- Lead time shortened from 21 days to within 15 days
- Improved EMI performance and PCB layout optimization recognized by end users
5. KKPCB’s Advantages in This Case
As a professional manufacturer dedicated to zero-defect PCB and PCBA services, KKPCB offers the following key advantages:
- High-precision SMT and DIP assembly for high-density, power-intensive applications
- Full AOI and X-ray inspection to ensure batch consistency
- Compliance with IPC-A-610 standards for industrial-grade durability
- Quick prototyping and small-batch ramp-up support
- BOM optimization and cost reduction analysis for better competitiveness
6. KKPCB’s Manufacturing-Focused Customized Solution
KKPCB provided a tailored solution that emphasized manufacturability and process reliability, including:
- PCB Stage: Used high thermal conductivity FR-4 material and optimized copper trace design to enhance heat dissipation.
- PCBA Assembly: Introduced selective soldering for power components to improve joint strength and consistency.
- Thermal Optimization: Re-positioned MOSFETs and regulators to reduce hotspots and ensure thermal balance.
- Flexible Production: Supported rapid transition from prototype to small batches for faster validation.
- Custom Testing: Designed an automated test jig to validate voltage/current response in every unit.
- Traceability: Implemented unique QR codes per board for end-to-end material and quality traceability.
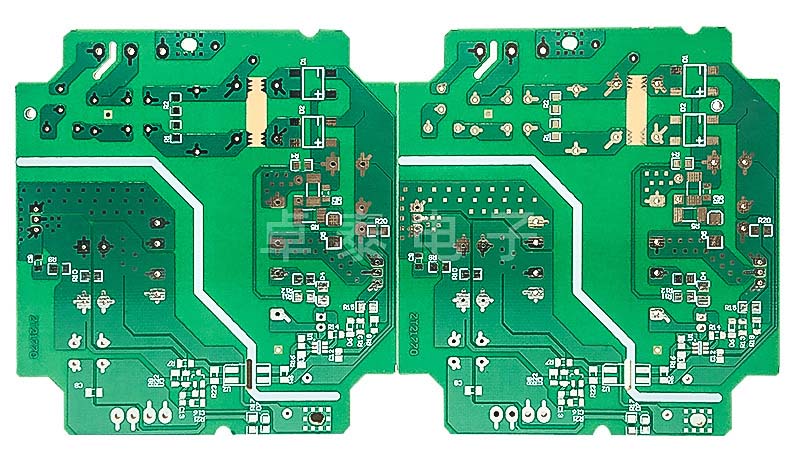
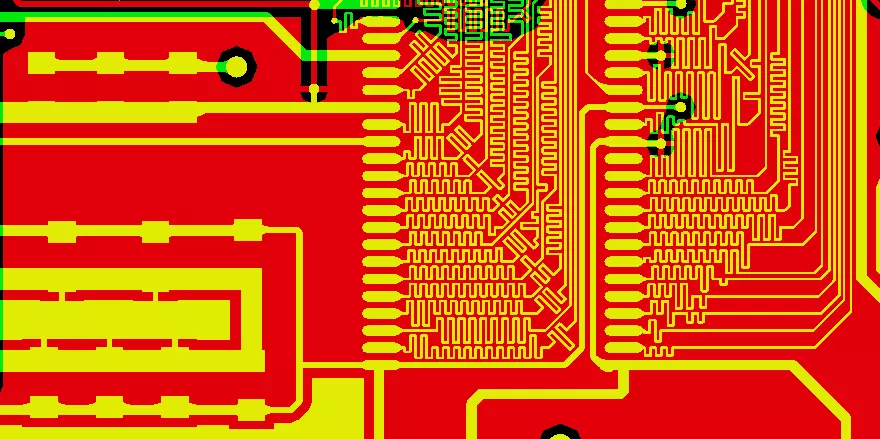
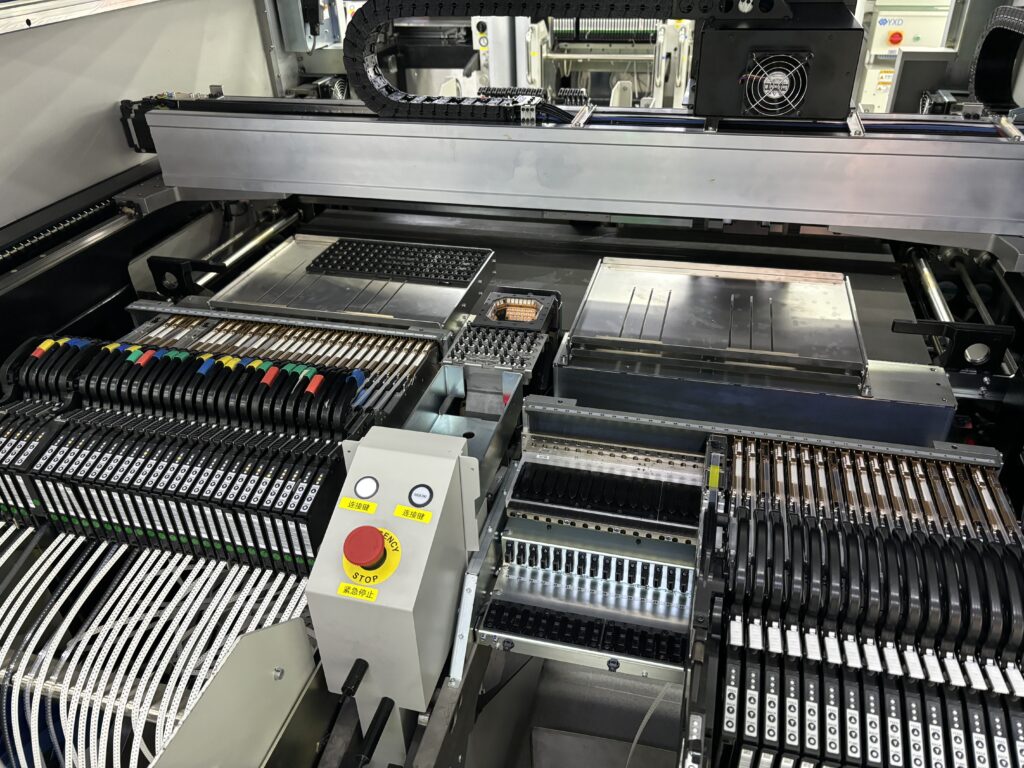
7. Measurable Impact of the Solution
Once deployed, the new PCBA solution brought measurable improvements:
- System failure rate dropped by over 60%, especially under 24/7 full-load conditions
- Passed third-party EMC testing on the first attempt, enabling faster market entry
- Helped the client save around 18% on annual procurement costs, improving product margins
- Lead time from prototype to mass production reduced by over 40%, accelerating the go-to-market pace
KKPCB – Your Zero-Defect, Reliable PCBA Manufacturing Partner in Industrial Automation.
Reach out today for your custom solution.