Industrial Motion Sensor PCBA Solution Case Study
1. Background Overview
In industrial automation systems, sensors play a vital role in enabling intelligent monitoring and equipment interaction. A European client recently sought to develop a PIR-based motion sensor module for use in equipment activity detection and control systems. The module required high sensitivity, strong anti-interference capability, low power consumption, and stable performance in harsh industrial environments. KKPCB provided a one-stop solution covering both PCB fabrication and PCBA assembly, ensuring fast, reliable, and cost-effective manufacturing.
2. Application Scenarios
This motion sensor module is designed for various industrial applications:
- Smart Lighting Control: Activates/deactivates lighting based on human or machine movement;
- Security Monitoring: Detects unauthorized motion in unmanned zones;
- Equipment Status Detection: Monitors robotic arms or AGV activity for logic control;
- Energy Management Systems: Optimizes HVAC and other utilities based on occupancy detection.
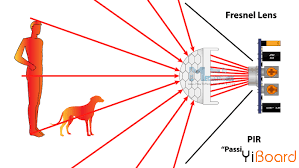
3. Product Specifications (Table Format)
Parameter Category | Specification |
---|---|
Sensing Technology | Passive Infrared (PIR) |
Operating Voltage | DC 3V–5.5V |
Operating Current | < 45μA @3V |
Detection Range | Up to 8 meters (typical) |
Detection Angle | Horizontal 110° |
Response Time | < 2 seconds |
Output Format | Digital Output (High/Low) |
Operating Temperature | -20°C to +60°C |
Module Dimensions | 22.7mm × 10.5mm |
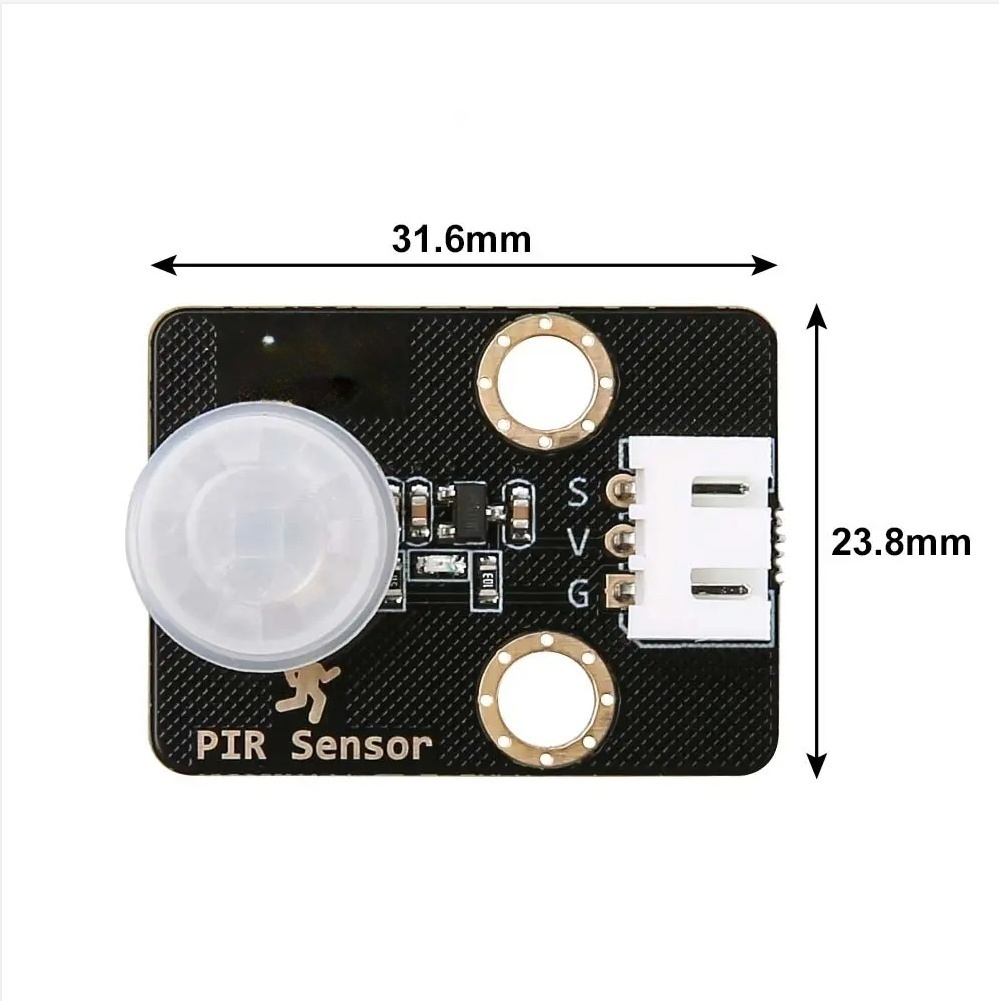
4. Application Results
Optimization Area | Results |
---|---|
Performance | Detection sensitivity improved by 15%; better anti-interference in noisy environments |
Cost Reduction | ~12% cost savings by optimizing BOM and using locally sourced components |
Delivery Time | Prototype-to-small batch delivery in just 12 working days (5 days faster than previous supplier) |
Quality | 100% functional test pass rate; failure rate < 300 DPPM in pilot batch |
5. KKPCB Advantages Highlighted in This Project
KKPCB demonstrated its strength as a trusted, zero-defect PCBA manufacturer through:
- Advanced SMT & DIP production lines supporting 01005, QFN, BGA, and more;
- Flexible prototyping to small/medium batch delivery, covering R&D to pilot runs;
- Bilingual engineering support (English/Chinese) for efficient communication;
- Comprehensive AOI, X-ray, and functional testing to ensure zero-defect delivery;
- Value-added component localization service to reduce sourcing risks and costs.
6. KKPCB’s Custom Manufacturing Solution (Focused on PCB & PCBA Execution)
For this client, KKPCB’s tailored manufacturing solution included:
- PCB Design Optimization Suggestions: Recommended high CTI base material for high-impedance input circuits and enhanced grounding layout to reduce noise;
- Refined PCBA Process: Adopted low-temperature solder paste and tight reflow temperature control to protect sensitive components;
- Customized AOI + Functional Test Jig: Ensured digital output logic worked reliably across all units;
- Fast Prototyping & Split Delivery: First prototype completed in 5 days; 1,000 pcs delivered within 10 days after confirmation;
- Component Replacement Service: Helped the client replace high-cost imported components (e.g., MCU, LDO) with equivalent domestic options, ensuring consistent performance at a lower cost.
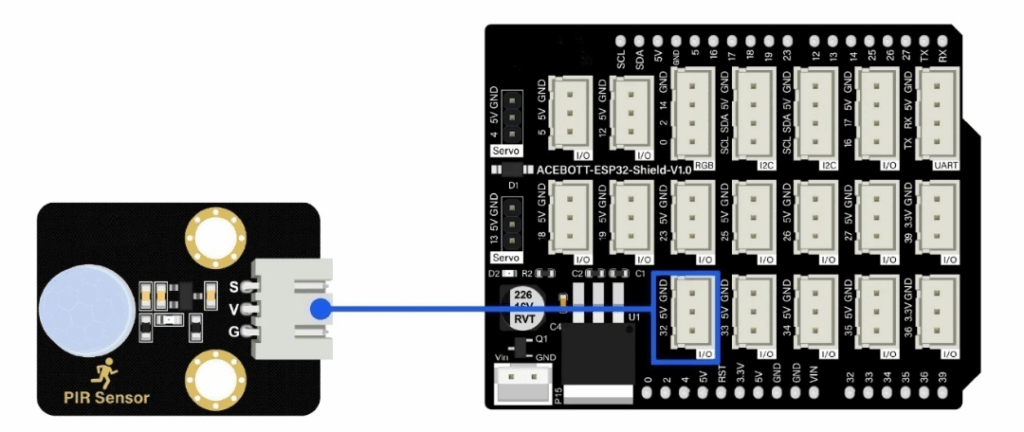
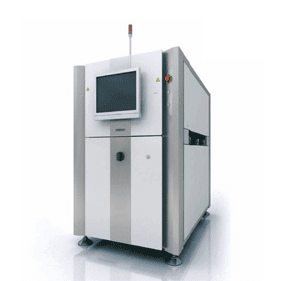
7. Real-World Outcome of the Solution
The delivered PCBA solution brought measurable improvements:
- Quality: Passed 72-hour aging and temperature cycling tests at client site; 100% acceptance rate, no returns;
- Performance: 15% improvement in sensitivity; false trigger rate reduced by approx. 30%;
- Cost Efficiency: 12% cost savings thanks to localized sourcing and manufacturing optimization;
- Lead Time: Reduced delivery cycle to 12 working days, ~30% faster than previous supplier;
- Supply Chain Reliability: All key components are now sourced in China, avoiding EU supplier shortages and delivery uncertainties.
Онлайн-магазины+и+маркетплейсы
May 13, 2025KKPCB seems to be a highly specialized and reliable company in the PCB and PCBA manufacturing industry. Their focus on high-difficulty and small to medium batch production is impressive, especially with the emphasis on high precision and fast turnaround times. The fact that they offer tailored solutions for specific client needs shows their dedication to customer satisfaction. I’m curious about how they manage to consistently deliver high-reliability products while maintaining such efficiency. Their in-house capabilities and one-stop shop approach must be a significant advantage in this competitive market. How do they ensure the quality and reliability of their products across such a wide range of applications? I’d love to hear more about their quality control processes and how they handle complex technical requirements. Do you think their solutions could be scaled for larger production batches without compromising on quality?
One-stop PCB Manufacturing and PCB Assembly solutions Manufacturer
May 26, 2025Thank you for your insightful questions! At KKPCB, we ensure consistent high reliability and efficiency through our comprehensive in-house capabilities, allowing tight control over every production stage—from design and material selection to assembly and rigorous testing. Our quality control processes include adherence to IPC standards, advanced inspection methods such as AOI and X-ray, and continuous monitoring via our MES system to maintain traceability and minimize defects. For complex technical requirements, our experienced engineering team works closely with clients to customize solutions tailored to their specific needs. Regarding scalability, our flexible production lines and robust quality management systems enable us to scale up to larger batch sizes while maintaining the same high standards, ensuring no compromise on product quality.