KKPCB Manufacturing Case: Mass Production Solution for Military-Grade Rugged Computer PCBs
1. Customer Requirements & Background
Industry: Defense Electronics
End Applications:
- Armored vehicle main control units
- Field communication relay equipment
Manufacturing Challenges:
- Heterogeneous material processing (AlSiC metal substrate + FR4 multilayer hybrid lamination)
- Extreme environment reliability (MIL-STD-810H vibration compliance)
- Military-grade quality control (100% inspection + batch traceability)
Previous Supplier Pain Points:
✔ AlSiC substrate yield only 65% (delamination due to CTE mismatch)
✔ PCIe gold finger contact failure rate 3,000 PPM (post-vibration)
✔ EMP shielding layer vacuum lamination yield below 80%
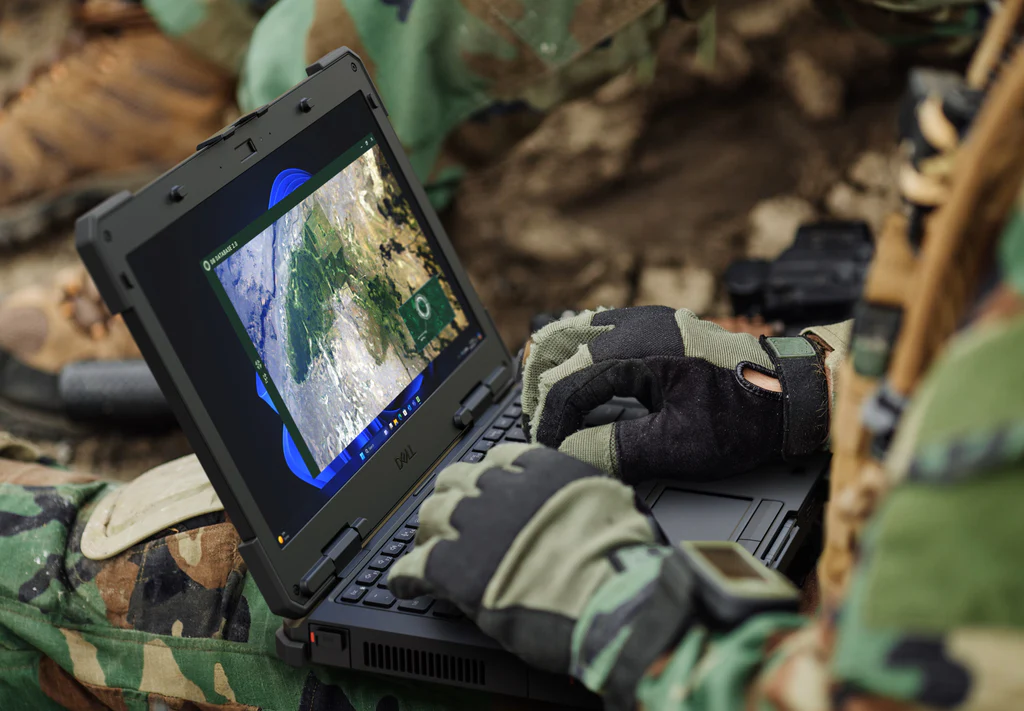
2. Core Manufacturing Capabilities
(A) Special Material Processing Techniques
Process Challenge | KKPCB Solution | Key Parameters |
---|---|---|
AlSiC-FR4 hybrid lamination | Stepwise thermoforming | 85±3t pressure, 2°C/min ramp rate |
Triple-redundant PCIe assembly | 6-axis robotic alignment | Coplanarity <0.05mm, Z-axis ±5μm |
Graded shielding vacuum lamination | Multi-stage vacuum degassing | Residual pressure <5Pa, parallelism ±0.3° |
(B) Dedicated Production System
Military-Spec Line Configuration:
- Temperature/humidity controlled workshop (23±1°C, 45% RH)
- Full-process ESD protection (human body voltage <50V)
Process Controls:
- Real-time SPC (CPK ≥1.67 for critical parameters)
- Laser QR code traceability (individual board production logs)
3. Mass Production Efficiency Gains
(A) Process Optimization Results
Metric | Industry Avg. | KKPCB Result | Improvement |
---|---|---|---|
AlSiC substrate yield | 65% | 98.7% | +52% |
PCIe connector failure rate | 3,000 PPM | 87 PPM | -97% |
Daily output | 40 panels/line | 120 panels/line | 200%↑ |
Rush-order lead time | 14 days | 72 hours | 80%↓ |
(B) Quality Validation Data
- 3 consecutive zero-defect batches (Lot size: 500pcs)
- 1,500-hour vibration aging test – zero functional degradation
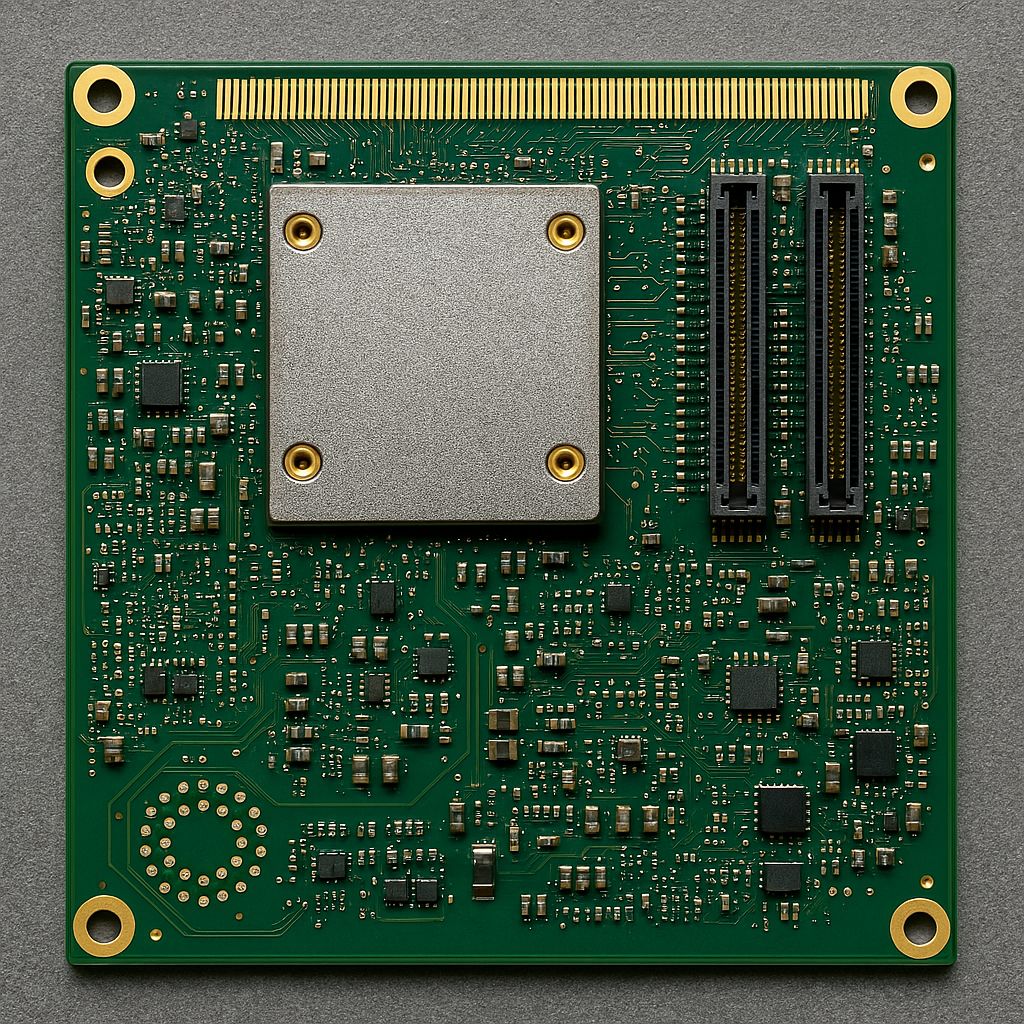
4. Manufacturing Technology Barriers
✔ Heterogeneous Material Bonding Technology:
- Proprietary AlSiC micro-etching (Ra=0.8-1.2μm)
- Interlayer adhesion >1.8N/mm (30% above MIL standard)
✔ Military-Grade Precision Assembly:
- Dedicated connector jigs (±3μm repeatability)
- X-ray + BGA red-dye dual inspection
✔ Extreme Environment Simulation:
- In-house vibration chamber (5-2000Hz, 50G acceleration)
- Climatic-composite test chambers (combined temp/humidity/vibration)
5. Production Showcase
(A) Military Production Line Layout (Photo Recommended)
[Pre-treatment] → [Auto Hybrid Lamination] → [Precision Assembly]
↓ ↓ ↓[Vacuum Lamination] → [Mil-Spec Cleaning] → [Conformal Coating]
Note: Independent material flow, showcase automated equipment clusters.
(B) Process Comparison (SEM Microscopy Recommended)
- Industry Standard: Micro-cracks at AlSiC interface (500×)
- KKPCB Process: Void-free bonding (500×)
(C) Traceability System UI (Screenshot Suggested)
QR scan reveals: Lamination curves / Test reports / Operator IDs
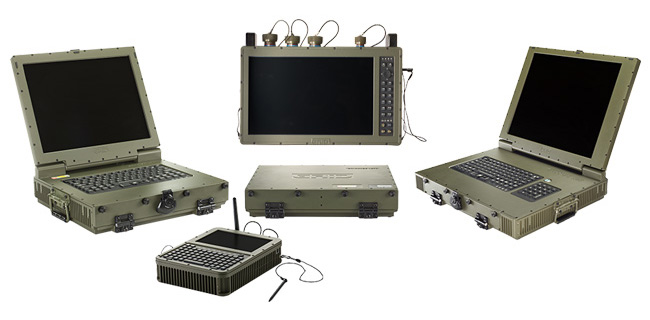
6. Customer Value
✔ Cost Reduction: 39% lower unit cost (via material utilization)
✔ Delivery Assurance: 500-panel safety stock for military orders
✔ Quality Commitment: 36-month extended warranty
7. Certifications & Services
◼ Compliance:
- MIL-PRF-31032 certified line (Cert#: KK-MIL-2287)
- IATF 16949 automotive-grade QC adaptation
◼ Value-Added Services:
- ITAR-compliant covert packaging
- 24/7 engineering support
Client Testimonial:
“KKPCB achieved 99.3% first-pass yield in initial mass production—far exceeding our expectations.”
— SQE Manager, Defense Contractor
Contact info: [email protected]