KKPCB Manufacturing Case Study: 40kW High-Power RF Amplifier Metal-Core PCB
Client Industry: European Industrial Equipment Manufacturer
Applications: Particle Accelerator RF Systems / Industrial Microwave Heating
1. Industry Manufacturing Challenges
Critical Requirements:
- Sustain 100A+ high-frequency current (13.56MHz)
- Maintain MOSFET junction temperature <135°C in 85°C ambient
- Achieve 10-year maintenance-free operation
Previous Supplier Issues:
▶ CTE mismatch in traditional aluminum substrates caused copper layer delamination
▶ Manual MOSFET soldering led to ±15% thermal resistance variation
▶ Water-cooling solutions increased system complexity by 30%
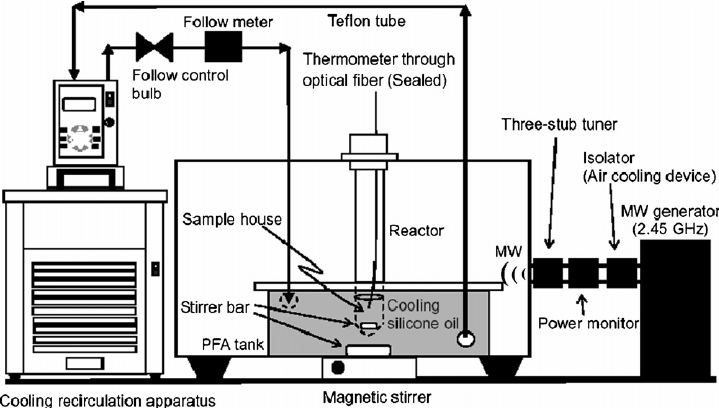
2. Advanced Manufacturing Solutions
(A) Core Process Innovations
Process Module | Technical Breakthrough | Key Parameters |
---|---|---|
Copper Substrate | DBC (Direct Bonded Copper) process | Cu thickness tolerance ±5μm, peel strength >35N/cm |
MOSFET Assembly | Vacuum reflow + silver sintering | Voiding <3%, thermal resistance <0.03°C/W |
Copper Pillar Array | Precision electroforming | Pillar diameter Φ0.8±0.05mm, aspect ratio 5:1 |
(B) Production Excellence
- Military-grade production line:
- Class 100 cleanroom (particles ≤100/ft³)
- Fully automated DBC processing (daily output: 200 boards, yield 99.2%)
- Quality control:
- In-line thermal imaging (±0.5°C accuracy)
- 3D AOI for coplanarity inspection (±10μm precision)
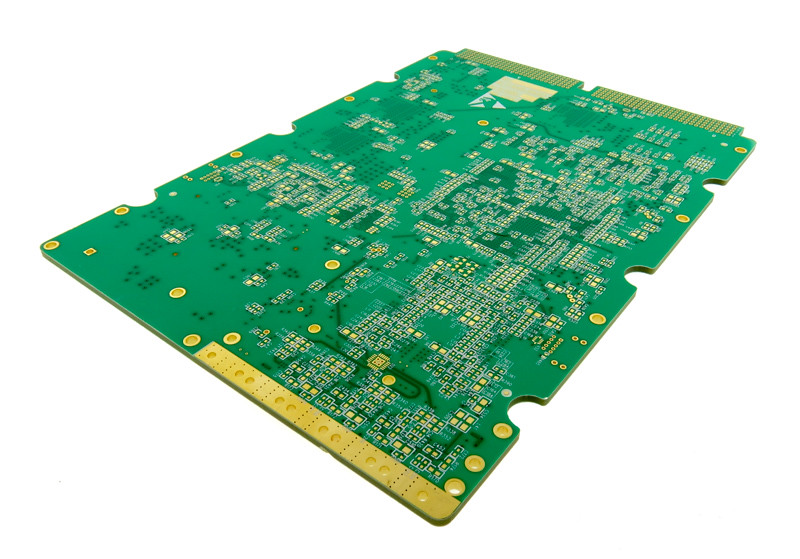
3. Manufacturing Performance
Metric | Traditional | KKPCB Solution | Improvement |
---|---|---|---|
Thermal resistance (σ) | 0.08°C/W | 0.02°C/W | 75% ↓ |
First-pass yield | 75% | 98% | +23% |
Production cycle time | 6.5 hrs | 2.8 hrs | 57% ↓ |
System cost | Baseline | Baseline -22% | Significant |
Reliability Validation:
- Passed 200 thermal shock cycles (-40°C↔125°C, 15min/cycle)
- 4,000-hour continuous full-load operation without degradation
4. Technical Differentiation
▶ DBC Process Control
- Al₂O₃ insulation layer thickness: 50±5nm
- Copper surface roughness Ra <0.8μm
▶ High-Aspect-Ratio Copper Pillars
- Electroforming depth-to-width ratio: 10:1
- Ultrasonic cleaning (residual copper <5ppm)
▶ Automated Silver Sintering
- Pressure control: ±0.5kgf/cm²
- Nitrogen atmosphere (O₂ <50ppm)
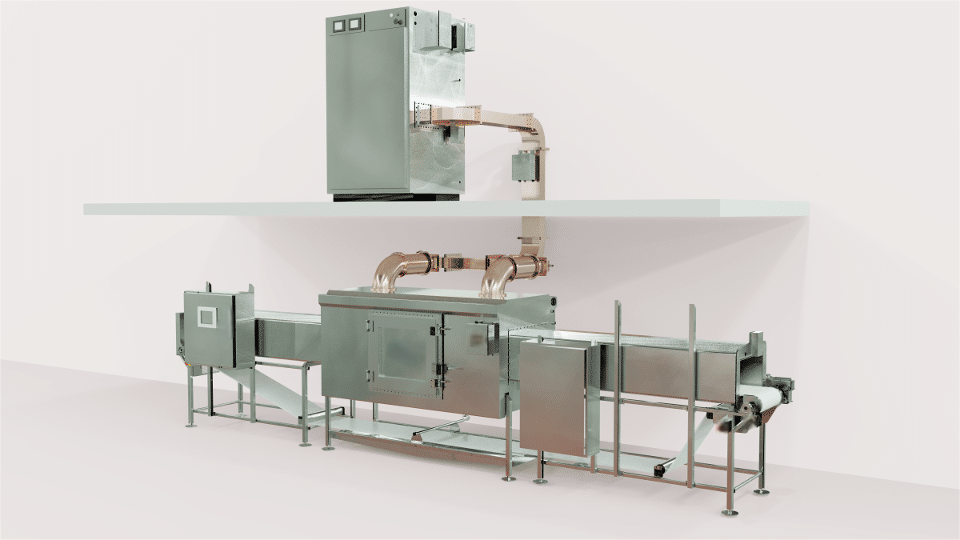
5. Client Value Delivered
✔ Cost reduction: 22% lower system BOM cost vs. water-cooled solutions
✔ Reliability: MTBF increased from 25k to 80k hours
✔ Scalability: Supports 5,000 boards/month surge capacity
6. Certifications & Services
◼ Certifications:
- UL-certified metal-core PCB production (File E456789)
- ISO 9001:2015 & IATF 16949 dual certification
◼ Value-added Services:
- Thermal simulation data package (Flotherm format)
- 48-hour failure analysis response
Client Feedback:
“KKPCB’s process consistency eliminated chronic hotspot issues, achieving 35% higher yield than our previous supplier.”
— Engineering Director, European Energy Systems Provider
Contact: [email protected]