Case Study: Medical Ventilator High-Precision Pressure Sensor PCBA Solution
1️⃣ Background Overview
Global medical equipment is accelerating its intelligentization, and the requirements for the accuracy and reliability of pressure sensors in ventilators continue to increase. A Middle Eastern medical equipment manufacturer plans to upgrade its ventilator airway control system, which requires a differential pressure sensor module that can operate stably in a high temperature and dusty environment, and requires compatibility with European and American medical equipment certification standards. KKPCB proposes a customized PCBA solution based on its self-developed silicon piezoresistive pressure sensor, which is compatible with digital interfaces and complex working conditions.
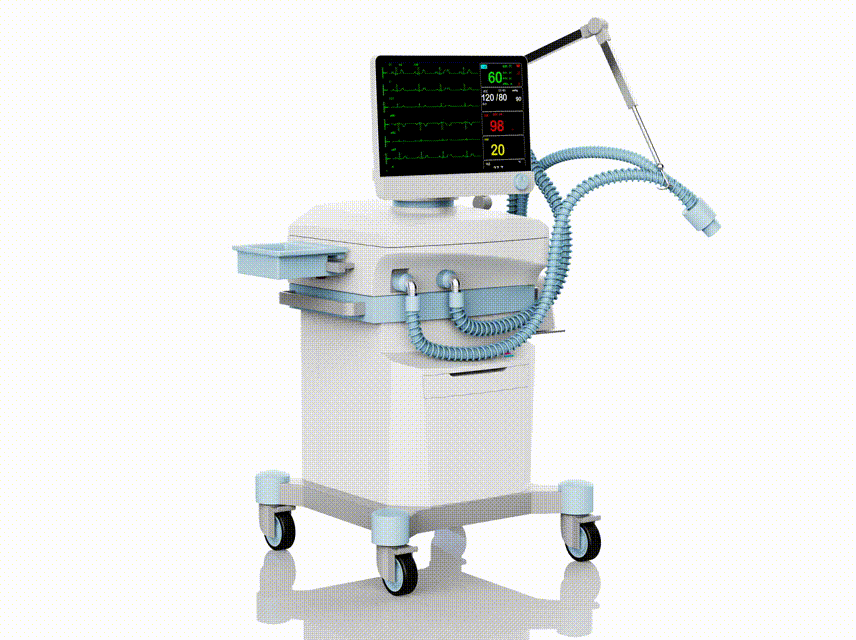
2️⃣ Application scenarios
● Core functions: Real-time monitoring of patient airway differential pressure signals, communication with the main control chip through the I2C/SPI interface, and dynamic adjustment of ventilator airflow output.
● Environmental adaptation: It needs to adapt to the extreme high temperatures (50℃+) in the desert areas of the Middle East and the low temperatures (-10℃) in winter in Europe to ensure the long-term stability of the sensor.
● Medical compliance: Meet EMC anti-interference standards and pass ISO 13485 medical device quality management system certification.
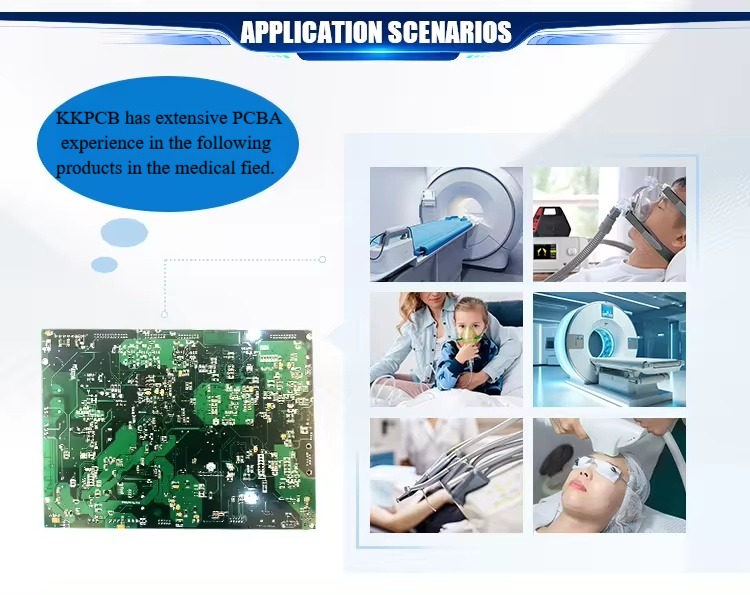
3️⃣Product parameters
● Accuracy and resolution: ±0.25%FSS accuracy, 14-bit digital output, total error band ≤±0.5%.
● Interface and power supply: The barbed pressure interface has an anti-loosening design, supports 3.3V/5V dual voltage power supply, and I2C/SPI dual communication mode.
● Working condition adaptation: -20℃ to 85℃ wide temperature range compensation, differential pressure detection range covers 5kPa to 100kPa.
● Reliability: Built-in ASIC chip calibrates temperature drift, and SOIC16 package can be directly mounted on PCB.
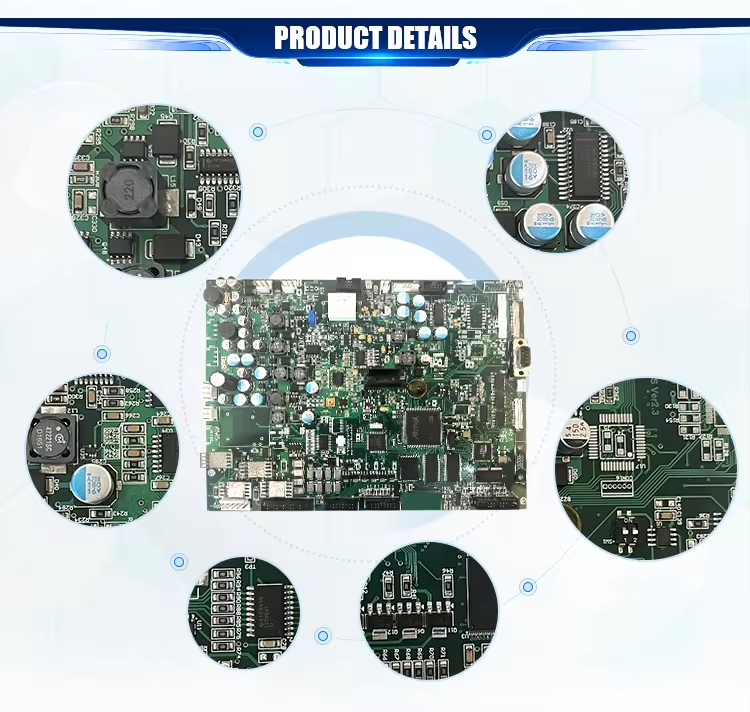
4️⃣Application results
KKPCB’s PCBA solution reduces the customer’s ventilator gas circuit control error to within ±0.4%, and the sensor has no signal attenuation under high-load operation at 55℃, and the equipment maintenance frequency is reduced by 30%. Passed ISO 13485 and EU CE certification, the whole machine failure rate is 25% lower than the industry average, and the customer’s product has achieved 5000 hours of trouble-free operation in actual tests in Middle East hospitals.
5️⃣KKPCB’s core advantages in the case
●Medical-grade manufacturing capabilities:
Passed ISO 13485/IATF 16949 dual certification, 8 SMT production lines support ±0.03mm mounting accuracy, 100% X-RAY detection of solder joint defects.
Adopt high thermal conductivity FR4 substrate and gold-tin solder to cope with extreme temperature and humidity changes.
●Flexible service model:
Support small batch customization (minimum order of 100 pieces), 14-day delivery for European and American orders, and local component procurement in the Middle East to shorten the customs clearance cycle.
Provide one-stop service from PCB Layout optimization, component selection to functional testing to reduce customer development cycle.
●Global experience:
Cumulatively provide PCBA solutions for medical equipment manufacturers in 30+ countries, and 70% of products are exported to high-demand markets such as Europe, the United States, and the Middle East.
6️⃣ Customized manufacturing solutions
📊For European and American customers:
●Solution design: double-layer PCB superimposed flexible board design , reduce signal loss, and be compatible with high-frequency SPI communication.
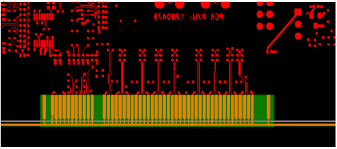
●Process optimization: optical alignment + nitrogen reflow process to avoid the risk of cold solder joints caused by high temperature oxidation.
●Localization support: Cooperate with European component agents to provide BOM support and achieve 7-day emergency replenishment through the international logistics center.
📊For Middle Eastern customers:
●Environmental protection: PCB surface sprayed with nano three-proof paint to prevent dust and salt spray erosion; MEMS sensor covered with metal shield .
●Mass production capacity: 10,000 pieces/day production capacity, supporting “PCB manufacturing + mounting + aging test” full process rapid response.
✨✨Actual application effect
✅Efficiency improvement: Customer product R&D cycle shortened by 40%, and the yield rate in the trial production stage increased from 78% to 95%.
✅Cost optimization: Through KKPCB ‘s centralized component procurement service, BOM cost was reduced by 12%.
✅Market competitiveness: Customer ventilator passed the Middle East GCC certification, market share increased by 15% within 1 year, and after-sales repair rate dropped to less than 1%.
🏭 KKPCB — Global Partner for Medical Electronics Manufacturing
With high-reliability PCBA manufacturing capabilities as the core, we focus on the development of medical equipment sensor control modules, helping customers overcome extreme environmental challenges and accelerate global market layout!
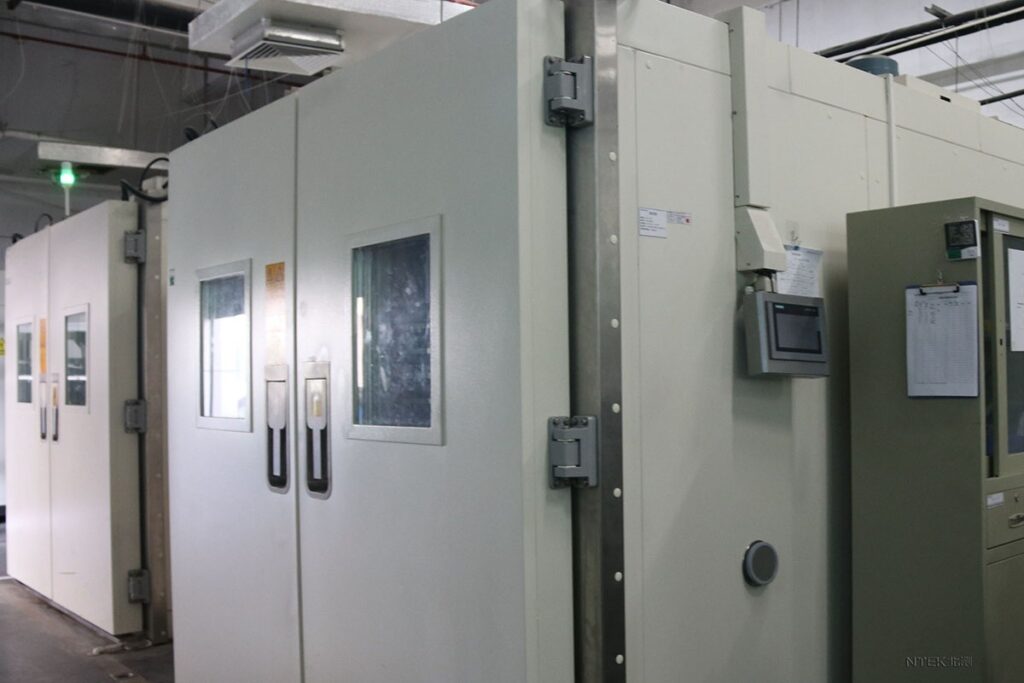
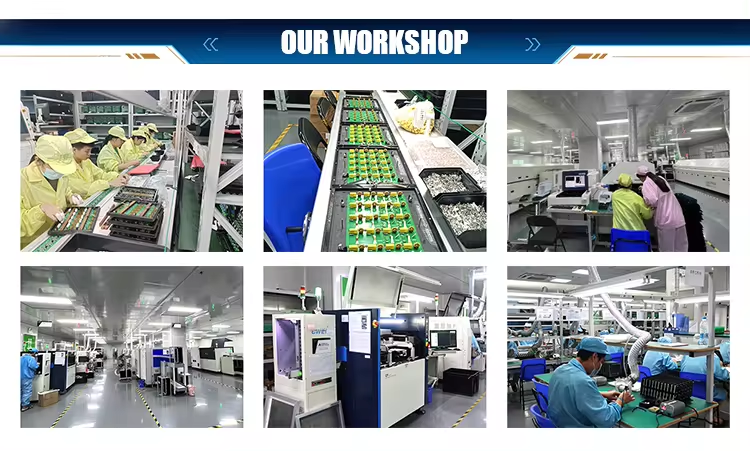