Motor Controller PCBA Solution for Industrial Automation
1. Background Overview
A European customer sought to develop a compact, high-performance motor controller for use in industrial automation systems. The controller had to support precise motion control, offer robust communication interfaces, and maintain operational reliability in demanding environments. Due to the complexity of the design and need for high-quality production, the customer turned to KKPCB for one-stop PCB manufacturing and PCBA assembly support.
2. Application Scenario
The motor controller is widely used in various industrial sectors including:
- Automated assembly and material handling systems
- Industrial robotics and AGVs
- Packaging and labeling machines
- Textile and printing equipment
- Servo drive systems in smart manufacturing setups
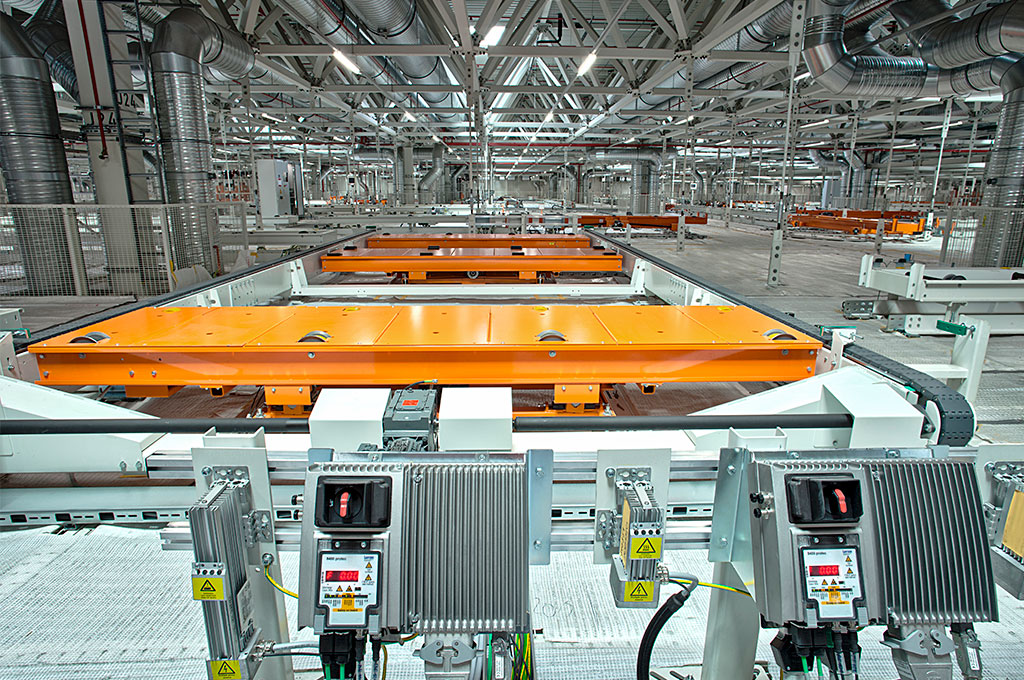
3. Key Specifications
Parameter | Specification |
---|---|
Input Voltage | 12V – 48V DC |
Output Current | Up to 30A continuous, 60A peak |
Motor Type Supported | BLDC / PMSM / Brushed DC |
Communication | CANopen / RS232 / PWM / SPI |
Control Mode | Speed, Position, Torque |
Protection Features | Over-voltage, Over-current, Over-temp |
Operating Temperature | -40°C to +85°C |
PCB Dimensions | 120mm x 100mm, 4-layer board |
Compliance | RoHS / CE / EN61800-5-1 |
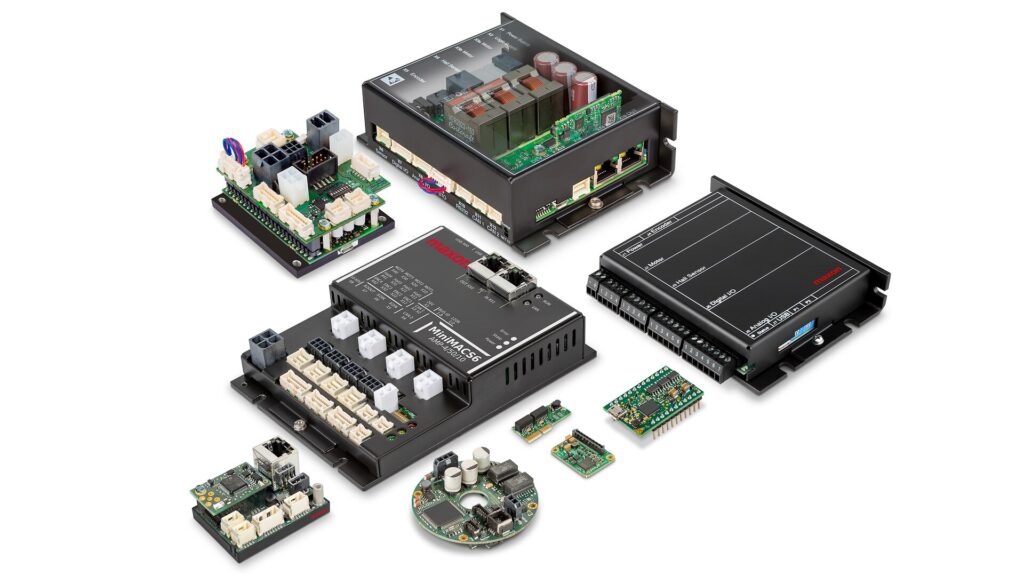
4. Results Achieved
With KKPCB’s manufacturing solution, the customer achieved:
- ✅ First-pass yield of 99.5%, a 2.5% improvement over their previous supplier
- ✅ Assembly cost savings of 15% due to optimized panel design and localized sourcing
- ✅ Lead time shortened by 20%, from 25 to 20 working days
- ✅ Signal noise reduced by 30%, enabling smoother motor operation
- ✅ Thermal reliability improved, passing 1000+ hours of thermal cycling without failure
5. KKPCB’s Strengths Demonstrated in This Project
KKPCB delivered significant value to the customer in the following ways:
- Deep expertise in complex multi-layer PCB fabrication, including impedance control and heat dissipation strategies
- Capability for double-sided SMT with BGA and fine-pitch components, ensuring consistent placement quality
- Full range of electrical testing (AOI, ICT, functional testing) to guarantee high reliability in motor control applications
- Flexible small-batch and rapid prototype manufacturing, ideal for customer validation cycles
- Strong supply chain management and localized component alternatives to reduce costs and lead time
6. KKPCB’s Manufacturing-Focused Custom Solution
Based on the customer’s needs and the challenges faced during prototyping, KKPCB provided a custom manufacturing solution grounded in PCB/PCBA expertise:
- PCB stack-up and thermal optimization: A 4-layer board was restructured with dedicated ground and power planes to reduce EMI and improve heat dissipation during high-current operation.
- High-current copper thickening: For better power trace reliability, 2oz copper was used on power layers, improving thermal and current handling without increasing board size.
- Component layout adjustment: Sensitive analog and digital sections were separated, reducing signal interference and enhancing control accuracy.
- Customized reflow profile: For a mix of large power packages and fine-pitch MCUs, a tailored thermal curve was used to ensure soldering consistency.
- High-reliability potting process: Select units were fully potted post-assembly for applications in vibration-heavy environments.
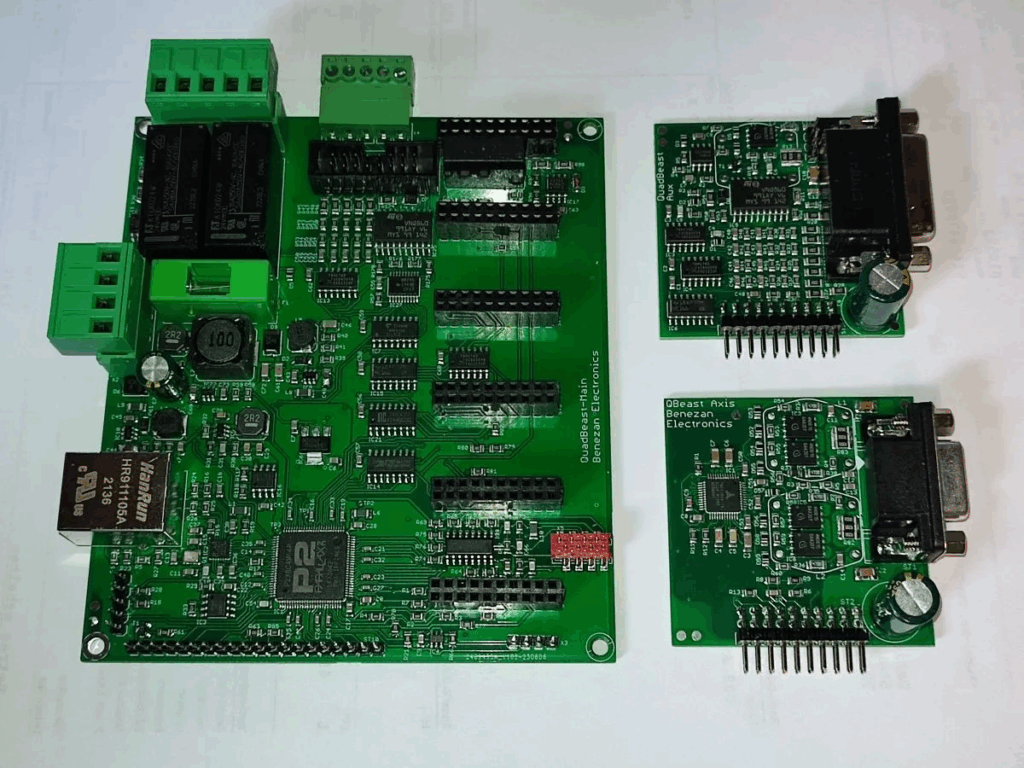

7. Practical Results After Implementatio
The customized solution delivered clear, measurable benefits:
- Quality: Solder joint reliability increased, verified by X-Ray and thermal shock tests. Field returns dropped to <0.15%.
- Cost: Panelization and component sourcing optimization cut PCBA unit costs by 15% without design compromise.
- Performance: Reworked layer design and copper thickness significantly improved EMI resistance and thermal behavior, reducing motor jitter and improving feedback accuracy.
- Delivery: KKPCB’s flexible manufacturing line shortened new batch delivery from 25 to 20 days, enabling faster customer deployment and better market responsiveness.
Investing
May 21, 2025Shenzhen KKPCB Technology Co., Ltd. seems to be a highly specialized and reliable manufacturer in the PCB and PCBA industry. Their focus on high-difficulty, small to medium batch production is impressive, especially with the emphasis on high-precision and fast turnaround times. The fact that they offer a one-stop solution for electronic manufacturing, including layout, assembly, testing, and verification, makes them a strong contender in the market. Their ability to handle complex designs and technical requirements is a clear advantage for customers in various industrial sectors. The mention of high-reliability products like Flex, Rigid-Flex, RF-Microwave, and HDI circuit boards highlights their expertise in advanced technologies. It’s also noteworthy that they provide all in-house solutions, which likely ensures better quality control and efficiency. How do they manage to maintain such fast turnaround times without compromising on the quality of their products?
One-stop PCB Manufacturing and PCB Assembly solutions Manufacturer
May 26, 2025Thank you for your interest! At KKPCB, we ensure fast turnaround without compromising quality by combining in-house engineering, precision manufacturing, and real-time MES production tracking—allowing us to tightly control every step from layout to final testing, especially for complex, high-reliability PCB products.