PCBA Solution Case Study for Industrial Robot Control System
1. Background Overview
With the growing adoption of industrial automation in Europe, an increasing number of companies are seeking compact, high-performance robot control systems to optimize production flexibility and operational efficiency.
A European client approached us with a demand for a next-generation industrial robot control system PCBA, aiming for smaller size, faster processing speed, enhanced communication capabilities, and better energy efficiency. However, they encountered key challenges, including PCBA cost control, high-frequency signal integrity, and ensuring consistent quality during scaling up for production.
2. Application Scenarios
- Compact industrial robots for assembly lines
- Collaborative robots (Cobots) in precision operations
- Automated guided vehicles (AGVs) and warehouse robots
- Medical robotics for laboratory automation
- Electronic device manufacturing and packaging systems
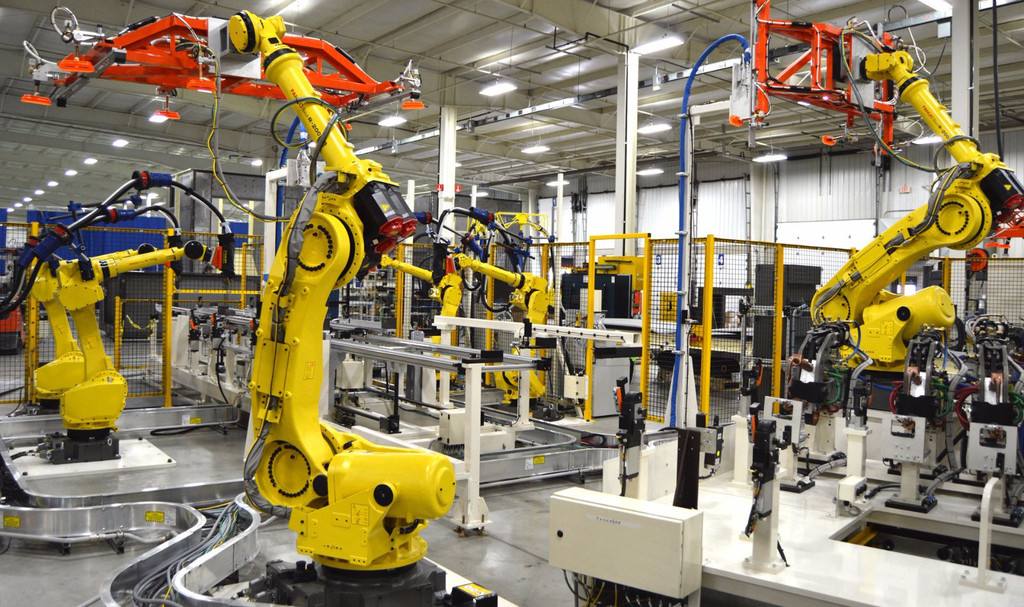
3. Product Parameters
Parameter | Specification |
---|---|
Input Voltage | 24V DC |
Main Processor | Industrial-grade ARM multi-core CPU |
Communication Interfaces | EtherCAT, PROFINET, TCP/IP |
Digital I/Os | 32 channels |
Analog I/Os | 8 channels |
Dimensions | Approx. 300 mm × 200 mm × 70 mm |
Operating Temperature Range | 0°C ~ 50°C |
Protection Level | IP20 |
Weight | Less than 4 kg |
Typical Control Cycle Time | Less than 4 ms |
Typical Payload Handling | Robots up to 10 kg payload |
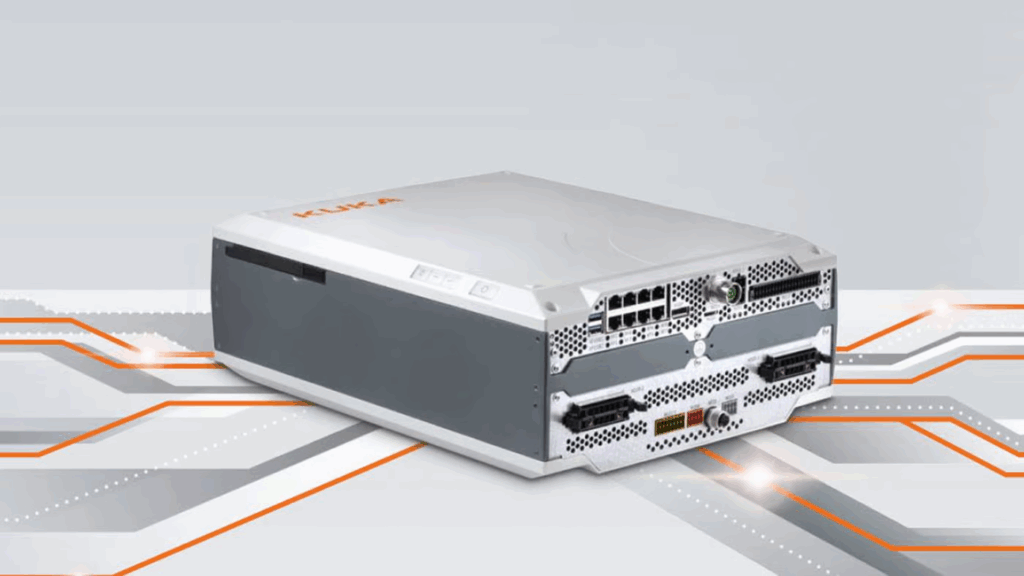
4. Application Results
Through a tailored PCBA manufacturing solution provided by KKPCB, the following results were achieved:
- Quality Improvement: PCBA first-pass yield increased to 99.95%, significantly reducing rework rates.
- Cost Optimization: Overall production costs reduced by approximately 8% through BOM optimization and streamlined manufacturing processes.
- Performance Enhancement: PCB signal integrity improved by over 20%, minimizing EMI issues and ensuring stable communication.
- Lead Time Acceleration: Mass production lead time shortened from 6 weeks to 4 weeks, with urgent prototypes delivered within 2 weeks.
5. KKPCB’s Advantages Demonstrated in This Case
KKPCB has a deep understanding of industrial automation requirements, and our experience ensured the success of this project.
We demonstrated our strengths through:
- Advanced PCB manufacturing capabilities with high precision for multilayer and high-density interconnect (HDI) boards.
- Full-process PCBA quality control including SPI, AOI, X-ray inspection, ICT, and functional testing.
- Rich experience in managing high-frequency and high-speed signal PCBAs, crucial for industrial robot controllers.
- Rapid prototyping and small-to-large batch manufacturing flexibility.
- Material sourcing stability, mitigating risks caused by global supply chain fluctuations.
- Compliance with ISO9001, ISO13485, and IATF16949 certifications for high-reliability applications.
6. KKPCB’s Customized Manufacturing Solution
For this industrial robot control system PCBA, KKPCB provided a comprehensive manufacturing solution focused on:
- PCB Manufacturing: Using high-TG, low-loss materials with controlled impedance designs to ensure stable and reliable high-frequency communication.
- PCBA Assembly: Implementing strict temperature profiles during reflow soldering to prevent voids and ensure solder joint reliability for fine-pitch components.
- Protective Coating: Applying conformal coatings to PCBA assemblies to resist moisture, dust, and chemical exposure.
- In-process Quality Control: Conducting multiple inspections (SPI, AOI, ICT, FCT) at every critical manufacturing stage to ensure near-zero defect output.
- Risk Management in Component Supply: Preparing safety stocks for critical components and offering proactive alternatives to reduce procurement risk.
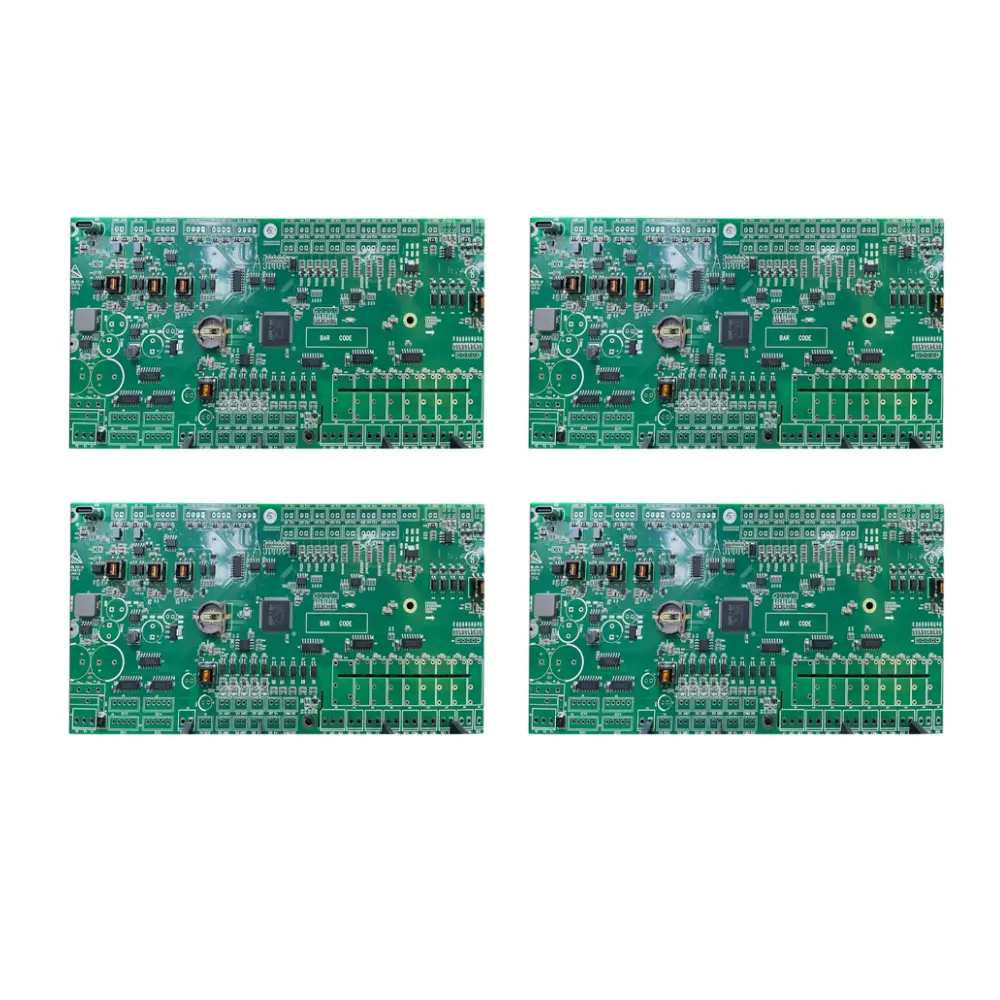
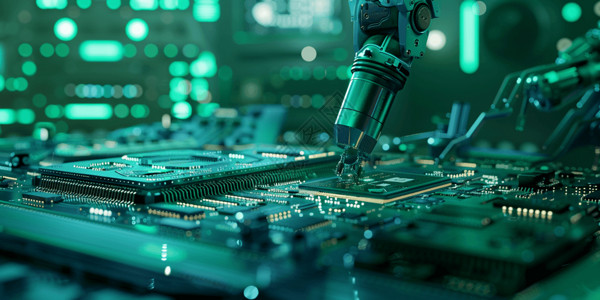
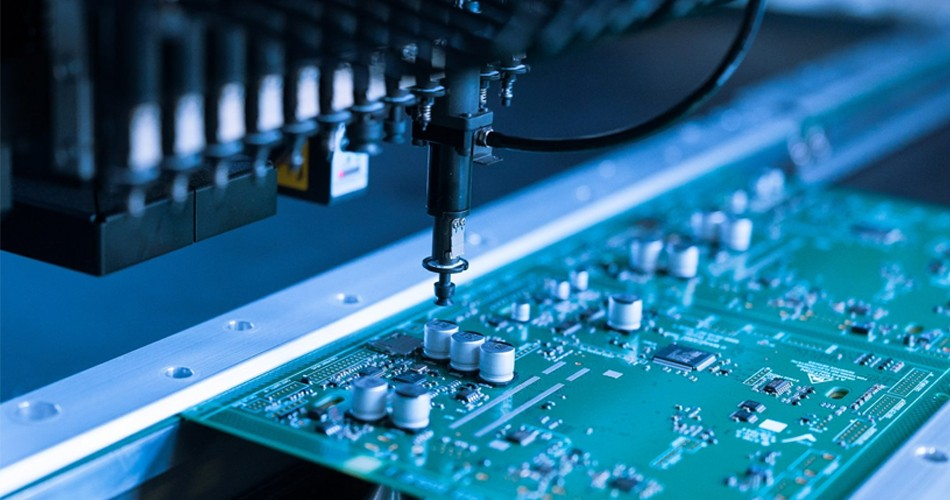
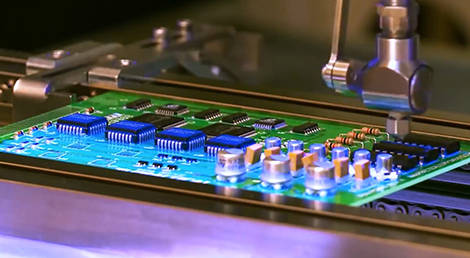
7. Actual Effects After Solution Implementation
Following the implementation of KKPCB’s customized solution:
- Quality Metrics: PCBA pass-through yield stabilized at 99.95%, leading to a 35% reduction in after-sales defects.
- Cost Savings: Total cost per unit dropped by 8%, helping the client maintain competitive pricing in the market.
- Performance Gains: EMI reduction of over 20% enhanced the communication stability of the control system, improving overall robot responsiveness.
- Faster Time-to-Market: Shorter delivery cycles (standard orders within 4 weeks, urgent orders within 2 weeks) enabled the client to accelerate their product launch schedule by at least 3 months compared to previous manufacturing arrangements.